In order to let the cable that goes in to the motor loose, I have to remove the motor cap on the disk brake side. Do I ?
Also ...Do I need to remove the hidden Snap-Ring in order to let the cap slide out ?
You should be able to remove the side cover first, and then remove the two circlips that are shown here:
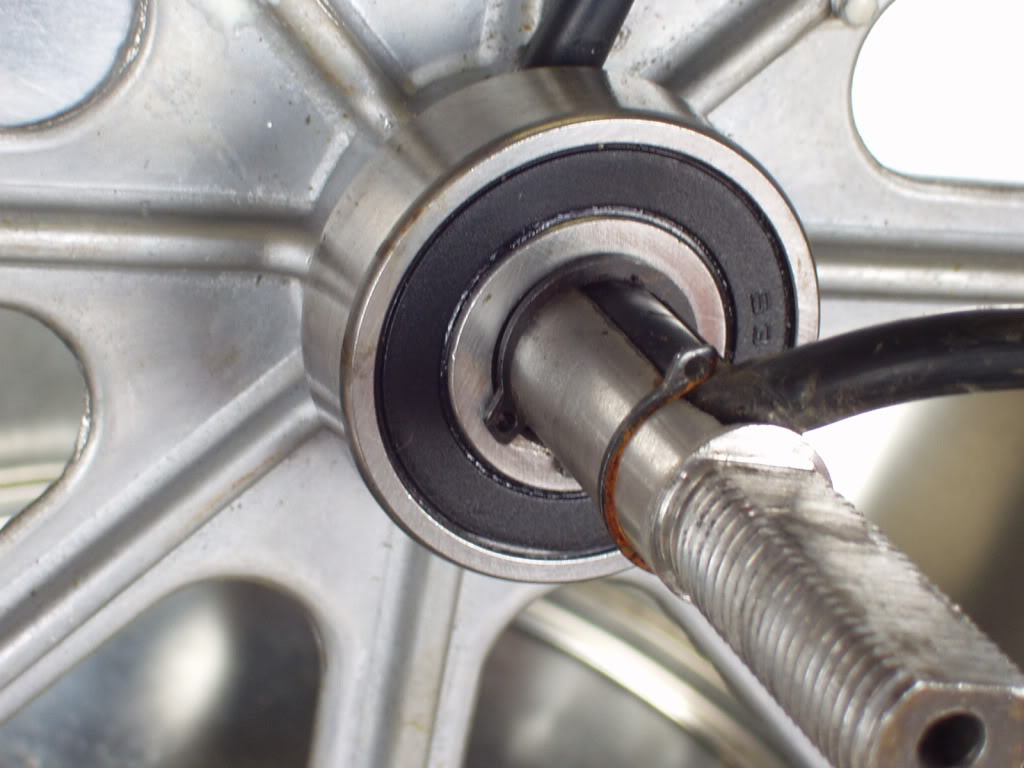
If it doesn't release from the bearing easily, you may need to use a hammer and a wooden drift from the opposite side, to gently persuade it to let go.
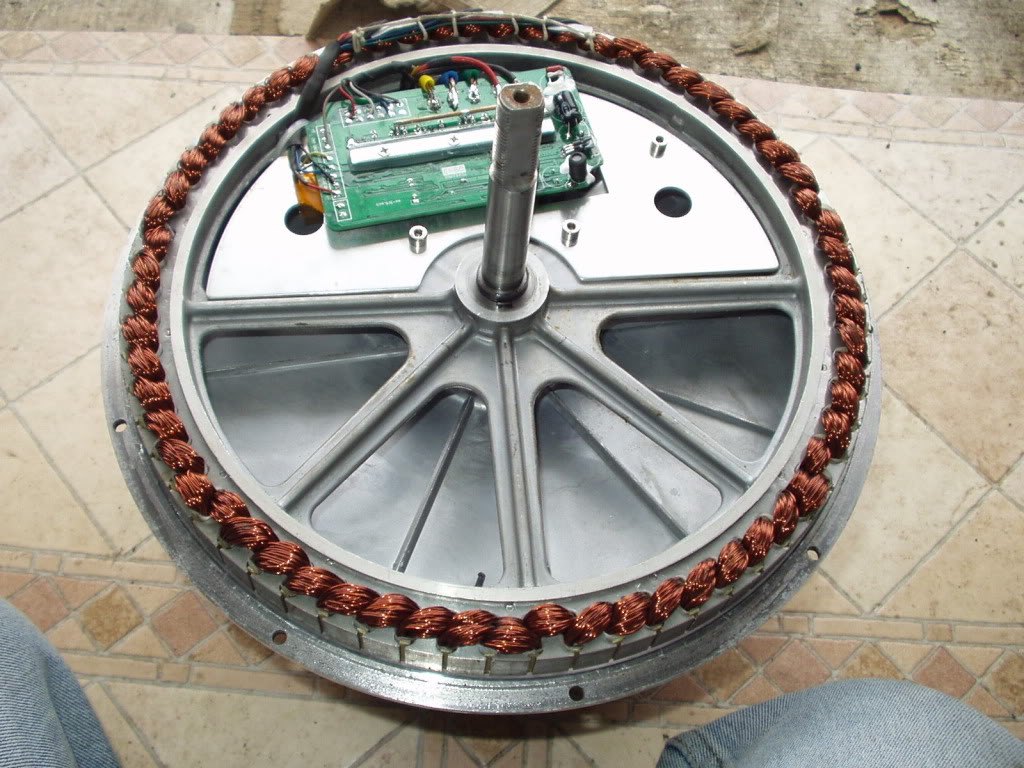
A piece of old broom handle or 1/2" dowel is ideal for this and should be positioned as close to the bearing as possible, gradually working around the eight openings in the stator to ensure the cover comes off evenly, otherwise it could tilt and jam.
If you can slide the bearing about 1/2" away from the stator
(you might need to lever it with a couple of screwdrivers or open ended spanners if it's too tight) it should make it much easier to pull the old cable through the narrow slot in the axle. Liquid soap
(or silicon spray etc.) can be applied to help it slide through more easily.
With the cable removed, use a small file
(or a piece of emery cloth) to remove any sharp edges from the slot before you attempt to pass the new wires through it.
You will need three lengths of heavy duty cable for the phase wires
(12g EcoWireâ„¢ Plus from Alpha Wire works well for this) and five thin wires for the hall sensor connections
(ribbon cable or network cable etc.).
If you use the same colour cable for all three phase leads, use a permanent marker to mark some indicator lines on both ends of the three new phase wire extension cables, so you can identify which is which when the wheel is assembled, ie G=I, B=II & Y=III.
Now you need to get all eight of these wires threaded through the slot and under the bearing with enough length to reach the wires on the stator.
Slide
(or gently tap) the bearing back against the stator, and then refit the two circlips taking care not to trap any of the wires.
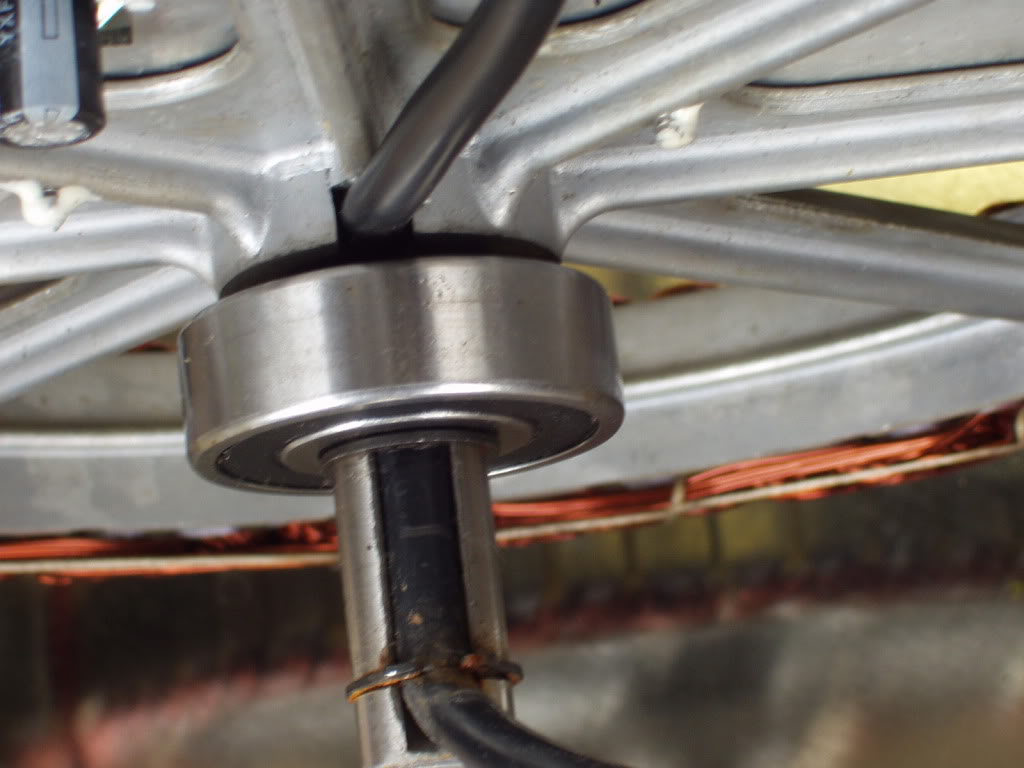
Solder and insulate each of the eight connections, and then make sure the wiring is secured to the stator with tie-wraps to ensure it cannot chaff against either the stator or the side covers.
Heat shrink tubing is probably the best method for insulating the soldered joints, but don't forget to slide it onto the wires as far as possible, before you solder the joints.

Fit the side cover and fixing bolts.
Fit the wheel, and then snip the wires to the required length before fitting some connectors to suit your new controller.
Alan