I checked the output of the charger and got a reading of 54.3V
The battery output voltage when on the charger is 52.8V
Ben, the voltage reading for the charger output appears to be within 0.5% of the expected voltage, but this lower than expected reading may be due to the accuracy of your multimeter
(cheap multimeters are usually accurate within ±1.0%).
If the charger output was calibrated absolutely spot on @ 54.60V, you could still have a voltage reading
(on a cheap multimeter) anywhere between 54.05V and 55.15V and still be within the meter's specified tolerance.

The 1.5V difference between the charger output and the battery output will be partially due to the slight voltage drop across two different sets of MOSFETs, one set on the charger input and the other on the battery output.
The main voltage difference is most likely due to the accuracy
(tolerance) of the individual cell maximum voltage settings for each of the 13 balancing modules within the
BMS, but it could also be slightly lower if some of the cells were not quite 100% fully charged.

If you were to leave your battery on charge for at least 24 hours to ensure precise cell balancing and a full charge has been achieved, it's possible that the battery output voltage reading
(measured while still on charge) might even increase slightly.
It is very unlikely that an expensive and highly accurate
BMS has been used with that battery, so you may have to simply accept that the output voltage of 52.8V is all that you are going to get.

52.8V is ~4.06V per cell, which should make the cells in your
free battery last quite a bit longer.

One thing I learned was that the big nuts loosen up after an initial installation. Seems the high torque on start up and regen works them back and forth. I had to tighten mine several times before they would remain tight. I still check them regularly, but they seem OK now.
Walter, most people don't understand quite how much torque is actually being transmitted through the two 10mm flats on the axle. If the axle nuts are not properly tightened they can work loose very quickly.
I measured the
stall torque on my modified Magic Pie and calculated it to be around 93Nm. If this force is exerted on a 10mm deep dropout the lateral force acting upon the end of the dropouts by the edges of the flats is probably around 950kg
(475 kg on each end of the axle).To visualise this amount of torque, if you were to place a 130mm long 10mm spanner onto the flats of the axle, you would have to apply a force of 73kg
(160lbs or 11.5 stone) on the opposite end of the spanner to produce 93Nm of torque!
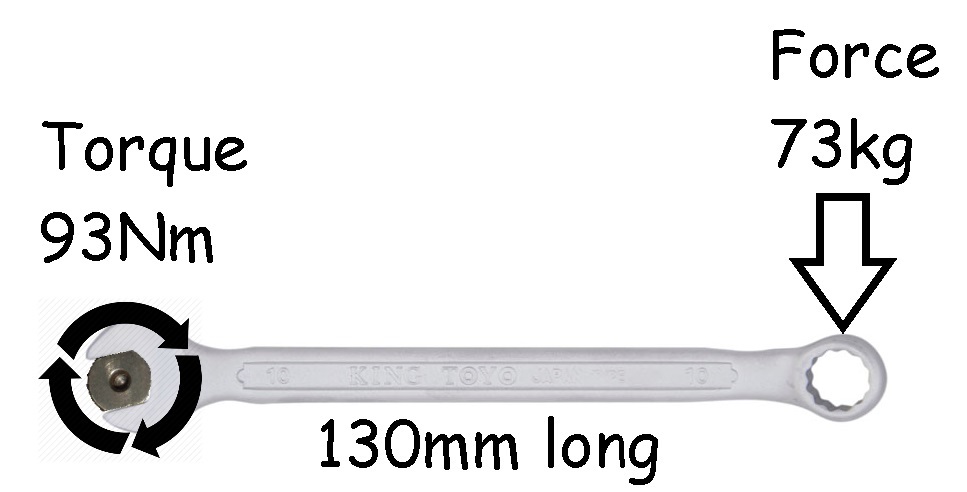
So Ben was lucky that it was only the hanger for the derailleur that broke and not his frame dropouts. If the dropouts in the frame had been deeper, then it might have been a different outcome.
I was never able to measure how much torque was produced with this much power:
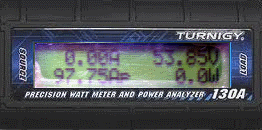
But the torque was enough to easily flip the bike over backwards when trying to pull away from a standstill on the level.
Fortunately, I had steel dropouts on my bike and the axle nuts were tightened very tightly indeed, and the dropouts survived the huge amount of torque even without any torque arms fitted.

The torque developed by your Smart Pie will obviously be a lot less than my modified Magic Pie
(and a bit less than a standard Magic Pie) but it still has to be transmitted safely to the frame
(or forks) through the dropouts.
Alan