Hi and

to the forum,
I don't think you are doing anything wrong but I suspect the controller has been set to allow a maximum of 380 rpm.
The controller is limited to an absolute maximum battery voltage of <63V (the maximum safe nominal battery voltage is 48-51.8V).
Even at the absolute maximum battery voltage, the motor's unloaded speed is unlikely to exceed 380 rpm, therefore there is not much point in allowing higher rpm figures to be entered.

A 26" wheel spinning at 380 rpm equates to ~47 km/h, so it shouldn't be the 380 rpm that is limiting your top speed.
It is more likely to be a low throttle signal voltage (below 3.25V)
or insufficient current being provided to achieve the maximum speed under load.
If you are unable to achieve the expected wheel rpm
(or speed) under a no load condition
(wheel suspended in mid air) then I suspect it is either the throttle itself, or more likely a low +5V supply from the controller.
If the +5V supply to the throttle is too low, then the throttle would be unable to output the 3.25V required to achieve maximum rpm.

You should be able to check the actual +5V supply voltage by measuring it in relation to battery negative
(ground) at the pedelec connector
or one of the brake switch connectors:
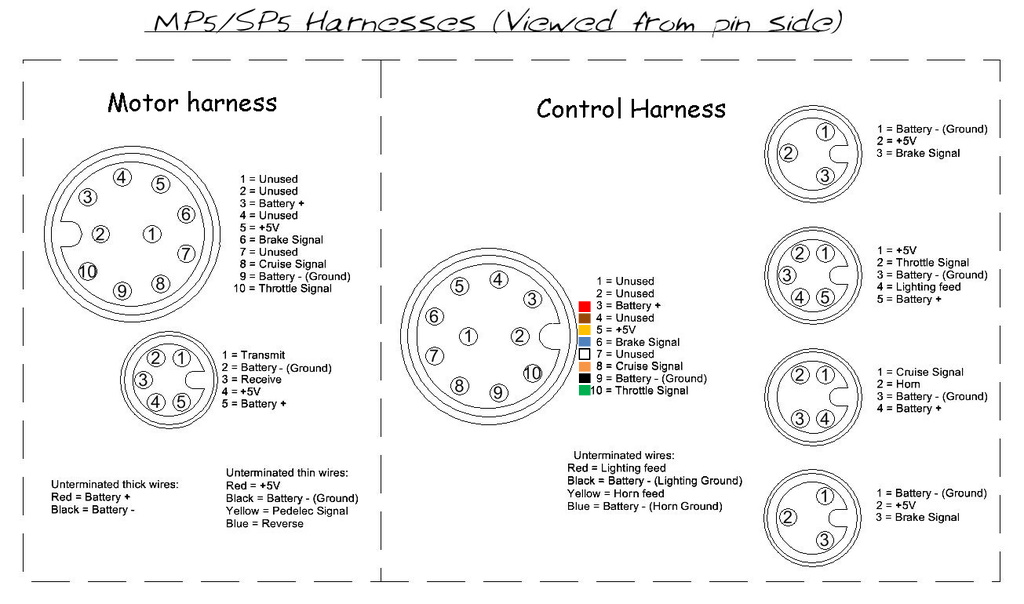
If you place a short piece of wire insulation on the end of the Positive meter probe
(or wrap some insulation or masking tape around it to make a tube) it will prevent the probe from accidentally touching against adjacent pins while you are checking the voltage on the +5V supply pin:


The +5V supply should ideally be between 4.5~5 Volts, but your throttle may still produce a full throttle signal output voltage
(at least 3.25V) with slightly less than 4.5V on the +5V supply.
P.S. I have just checked one of my controllers to see what voltage readings you should expect to see:
The +5V supply was reading a constant ~4.9V with the throttle and Bluetooth dongle disconnected.
When I plug just the throttle in, it drops to 4.23V.
When I plug just the Bluetooth dongle in, it drops to 4.52V.
When both units are plugged in, it drops to 4.22V
Please keep us updated with your findings as it may well help others who may be experiencing a similar lack of top speed.
Alan