I have not dismantled a Black Pie, but I would expect it to use the same bearings as the Magic Pie III, 4 and 5:
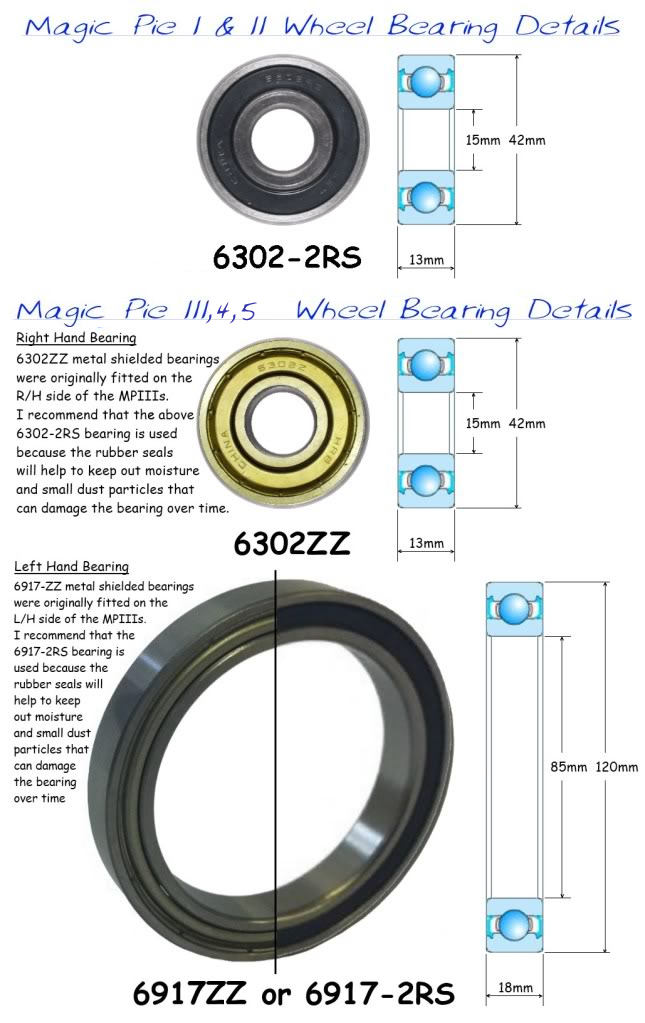
Many of the Magic Pies
(and Smart Pies) had a small amount of bearing play from new:
Most single ball race bearings will have some amount of sideways twisting movement, but as the two bearings on the Smart Pie are fitted very close to each other on the axle, this slight amount of movement in the bearings will be significantly exaggerated when observed at the rim.
It is common engineering practice to eliminate bearing movement by applying a small amount of sideways force to preload the bearings:

GM use a wavy spring washer to eliminate any end play and compensate for slight differences in the machining process of the individual components, but if you apply a small amount of sideways force to the rim, the washer will simply compress.
Replacing this wavy washer with a solid washer of the correct thickness should remove most of the play under normal loads, although if enough load is exerted, the side covers will probably flex enough to allow the movement to become visible again.
If the washer used is too thick, the preload on the bearings can be excessive, causing the bearings to wear out much quicker than normal.
I have noticeable movement on both my MPIII and my Smart Pie which has been there from new, but it is not enough to allow contact between any of the stationary and moving parts (the stator and magnets or the windings and the covers etc.) and it does not affect the operation of the wheel. If the play becomes bad enough to cause concern, I will rectify the problem then, but I am reluctant to pull it apart until I need to do so.
You know what they say, "If it ain't broke, don't fix it"! 
My Magic Pie Edge had several flat steel shims instead of the wavey washers to take out the movement in the bearings:
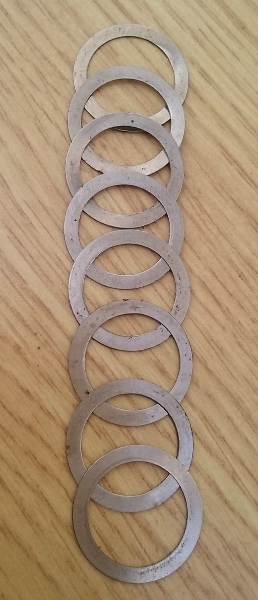
If your bearings are still smooth and quiet, adding some additional shims should eliminate any unwanted movement in the bearings.
If you can't find spacer shims of the correct size, you could apply some aluminium tape to one
(or more) of the existing shims to thicken them up and simply trim around the inner and outer edges of the shims with a sharp modelling knife to remove the surplus tape.
I have successfully used this method to produce thicker shims for setting valve clearances on my Toyota's new cylinder head, and it added ~0.006" in thickness for each layer of tape.
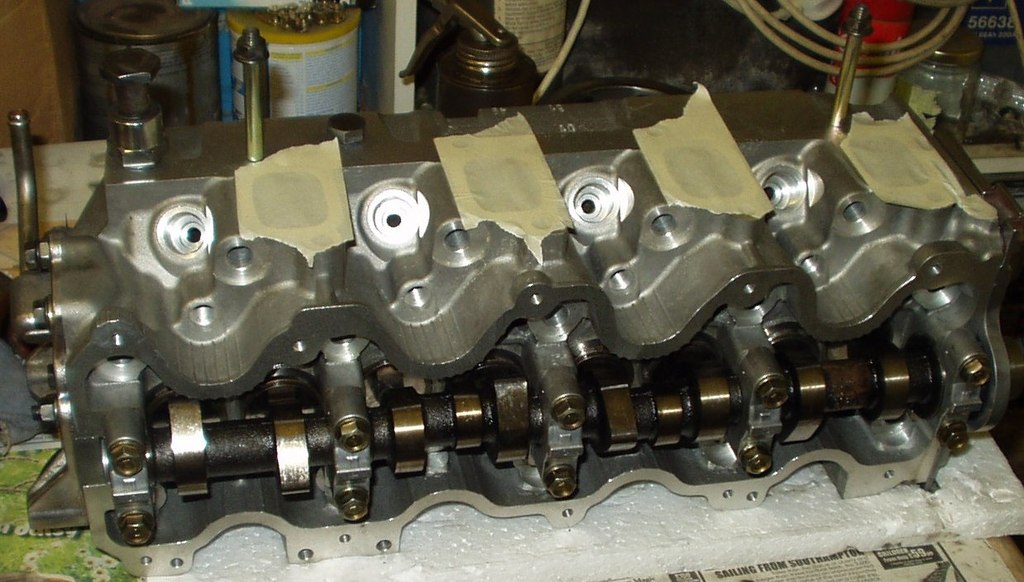
The aluminium tape was basically sandwiched between the shim and the bucket to ensure that it would not be worn away by the hardened steel camshaft.

The engine ran great for two years until the replacement cambelt
(the one that was supplied with the new cylinder head) decided to snap, bending some valves, and breaking the camshaft into four pieces. This resulted in the destruction of a perfectly good cylinder head. :'(
Alan