Hi Kris,
I'm curious as to where you downloaded your software from as it is very different to the current software on the GM site:
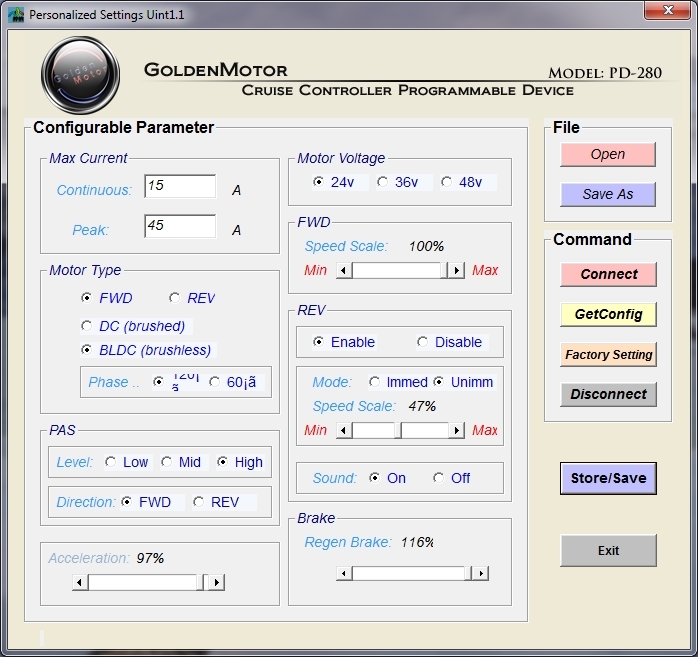

Which I discovered has a maximum regen setting of 116%.

I have now seen at least five different versions of the PD-280 software, but this one appears to be somewhat different to the others.
I'm guessing it could be for a wheelchair controller, as it does not support any of the pedelec (PAS) functions, or allow reverse to be disabled either.
In which case, the "Break Time" function probably should be "Brake Time", and may adjust how long the controller waits for the electro-mechanical brake to fully disengage before the motor is allowed to respond to the throttle input. This would prevent unnecessary load on the motor by trying to turn the wheel while the parking bake was still partially engaged.
As far as I can tell, the "Motor Voltage" setting is there to set the Low Voltage Cut-off point of the controller to prevent the battery from becoming overdischarged.
Most modern batteries
(apart from DIY LiPo packs) seem to have their own Battery Management System built in, so this setting is not usually necessary.
If the controller was factory set to 48V, users with 24V or 36V packs would not be able to use their motors without reprogramming them, and the USB leads are not always purchased with the wheel kits.
By having a factory default setting at 24V, users can simply plug in a 24V, 36V or 48V battery and use the motor straight out of the box without any need to change program settings.
I have all my controllers set to 24V to allow any of my battery packs to work with all of my motors, without having to reprogram the controller every time I swap batteries.
I suggest you try downloading the
latest software on the GM site and see if it can be used to adjust your regen to a usable level for your micro scooter.
Alan P.S. Check out
this link for more information on the Print Screen function.
