I had been thinking of doing that but I wouldn't have a clue what size resistor to use. also I would be a bit worried about to many volts on the controller in regen. I understand that you should not disconnect the battery when using regen as this can damage the controller to high a resistor may have the same effect. I did wonder if a zener diode across the pairs may prevent damage.
Thats easy.
E/I=R
Your pack voltage at full charge divided by your desired current.
Say 54v/5 amps is 10 ohms.
The regulator works well here.
The LM338 can limit the can limit the current by limiting the voltage when the load creates a voltage drop over a resistor on output and its adj leg.
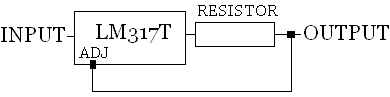
I would limit the current to 4.5 amps per chip but here it states with a big heat sink it will take 8 amps.
http://www.reuk.co.uk/LM317-Current-Calculator.htmHowever I'm unsure how the LM338 output is going to take the the battery input. So a Schottkey diode between the LM338 output and pack may be a good thing.
The above circuit is a current following mode design. A way to impede energy and power from regen fet to pack, and heat can be created away from the main circuit.
Works good for the 28" wheel that gives high current and lower RPM regen voltage,
A 16" wheel would benefit from a voltage regulator.
A more efficient approach would be to use an inductor. The motor is inductive power source and pulses energy power into the pack.
Boosting the voltage by creating magnetic fields from excess current can work as a current converter for regen to get the volts up to actually charge the pack.
And bucking can convert voltage into current.
Say a 16" wheel is spiking the fets with high volts in regen. You may need the topology right. So you put a buck on the phase wires to only work in regen.
Or the 28" wheel is creating too much current and its hitting on the motor, a boost can get your voltage from current.
How does regen work.
Interesting how even when the motor isnt spinning fast enough to create a viable charge voltage for the pack, it still causes resistance on the motor.
Wouldnt the lower RPM/voltage of regen in this situation cause current to still flow from the pack into the motor and regen causes current to flow from the motor to the controller?
IMO something in between is going to cop it.
Voltage only travels down hill regardless of the presence of current. And the current has nowhere to go unless it has a lower voltage before it. Yet we still see regen resistance on the motor at a snail pace.
Where is this current going if its not going into the pack?
This is where the NChannel may lets us down, It has a diode that provides a path the ground even when its off or on or reversed.
Using a Pchannel fet for regen may separate the motor from the pack when the regen voltage is lower, as the circuits path to ground should be blocked by the diode before the motor not after.
.
Something in the below picture doesnt look right.
Between the motor and pack there is a 16v difference and the fet when closed is allowing current to flow to ground. The voltage must manifest on the N channel gate or in the motor coil.
The resistance of the fet is lower than the pack and higher than the motor coils and the 120 amp fet should take much more current than the motor. I vote the coils are going to cop it.
This is set regen. So should it not deliver the same amps at low RPM but at a much lower voltage?
Im trying to understand the picture I drew below, can anyone fill in the blanks.
