I found another site that is quoting the max battery current of the VEC700 @ 96V is 400A. seems a little high given the other controllers maximums. Its much bigger than the others though, 330mm x 225mm. Worth taking with a grain of salt.
It is all too easy to simply assume that the manufacturer's stated maximum voltage and maximum current occur simultaneously, but we know this is not the case. I suspect the seller has inadvertently misinterpreted the facts he has been given.

I have also seen the VEC-700 controller advertised as 400A rated current and 700A peak, but does not specify that this is phase current and is dependant upon the voltage setting.
GM advertise the HPC700H square wave controller as 840A @ 48V:
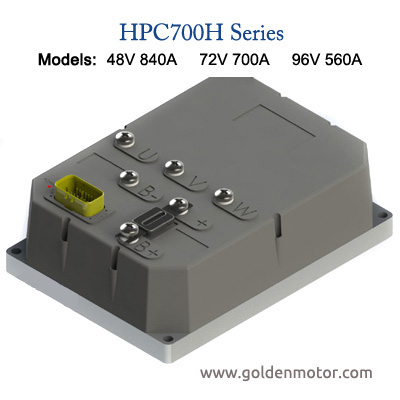
If this was actual Battery Amps, at the absolute maximum voltage of "~140V" that this controller can accept, drawing 560A from the battery would extract over 78kW of power from the battery.

This seems to be very high for a controller with a rating of just 30kW and typically used with a 20kW motor.
Using a large current controller with a low current motor could easily cause overheating, but I am also not sure how well the torque controlled throttle would work with a much smaller motor.

Phase current is typically higher than the battery current because it is being delivered in short intermittent pulses
(sine waves) directly from the capacitors in the controller. The battery experiences the average current being supplied to the controller's capacitors, so it is typically lower than the peak current supplied to the windings on each of the undulating pulses.
At lower motor speeds, the voltage in the windings is continually being turned on and off several thousands of times every second
(dependant upon the sine wave frequency), therefore the average voltage in the windings
(the Phase voltage) is effectively a lot lower than the battery voltage.
If a battery is supplying 10A @ 72V it is using 720Watts of power, then this same amount of power is transferred into the windings but at a much lower
average voltage.
If the maximum speed of the motor is 5000rpm @ 72V, it would need ~14.4V to maintain 1000rpm.
Presumably, if 720W of battery power was being drawn @ 1000rpm, the current in the phase windings
(at an average of 14.4V) would be 50A, which is 5 times the battery current.
In reality, the battery voltage x battery current = motor voltage x motor current, but minus the losses due to inefficiencies within the controller and power/phase cables.
Alan