Hi Roy, relying on the spring return of the throttle to shut of the power would be fine if problems never occurred, but real life is never that simple.
If water finds its way into the throttle unit
(or inside the throttle connector) the electrical conductivity of the water can alloy a full throttle signal voltage to be sent to the controller, even with the throttle fully released.

A dead-man's switch connected to the brake/power cut-off wires would be a good idea for typical braking use, but you might find it a bit annoying if you needed to change gear, scratch your nose or indicate a left turn with your left arm etc. while riding with power assistance up a steep hill.

It might be possible to use a micro-switch on the thumb throttle to activate the power cut-off function upon release, but this would still be a problem if the thumb throttle became stuck open due to a broken return spring etc.
The choice of battery is not as straightforward as you might imagine, as there are many factors that you may want to consider before deciding on which battery would be the best option for you:
- Battery cell type (LiFePo4, LiMn, LiPo or NiMh etc.)
- Battery style (rack mounted, frame mount, water bottle mount or seat post mount etc.)
- Battery capacity (8, 10, 12, 15 or 20Ah etc.)
- Battery size (physical dimensions) and weight
- Required range under power
- Ease of charging
- Number of expected charging cycles (life expectancy)
- Maximum and continuous current output
- Built in Battery Management System (BMS)
- Security
- Ease of removal and portability
- Safety
- Cost
People will obviously prioritise the above requirements differently according to their individual preferences and requirements.
I prefer cheap, high power and lightweight battery packs, and by fabricating my own packs it allows me to easily experiment with different voltages and much higher power outputs. I build my packs from readily available LiPo packs, but they require careful monitoring during charging
(using a special charger and power supply) and must also be safely protected against physical damage and excessive discharge current, as LiPo packs are renowned for turning themselves into
very effective incendiary devices.

Below is my latest compact, lightweight
(1.4 kg/3.09 lbs) battery pack, it's a 29.6V 5Ah
(33.6V fully charged) made from two
4s Turnigy LiPo hardcase packs, two
Turnigy watt meters, a
40 amp fuse, and a
plug in battery monitor unit, are all neatly contained within the
small frame pannier bag which is Velcro strapped to the front of the top crossbar for quick and easy removal:
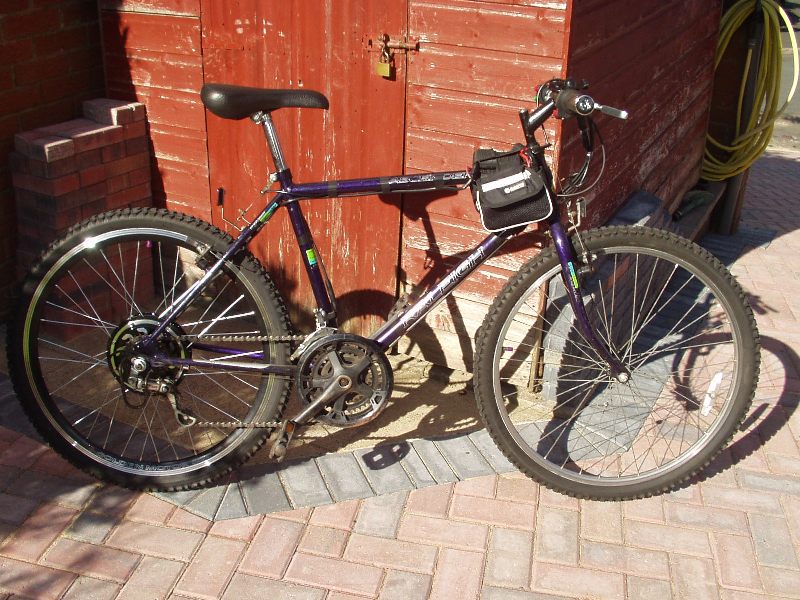
Size comparison:
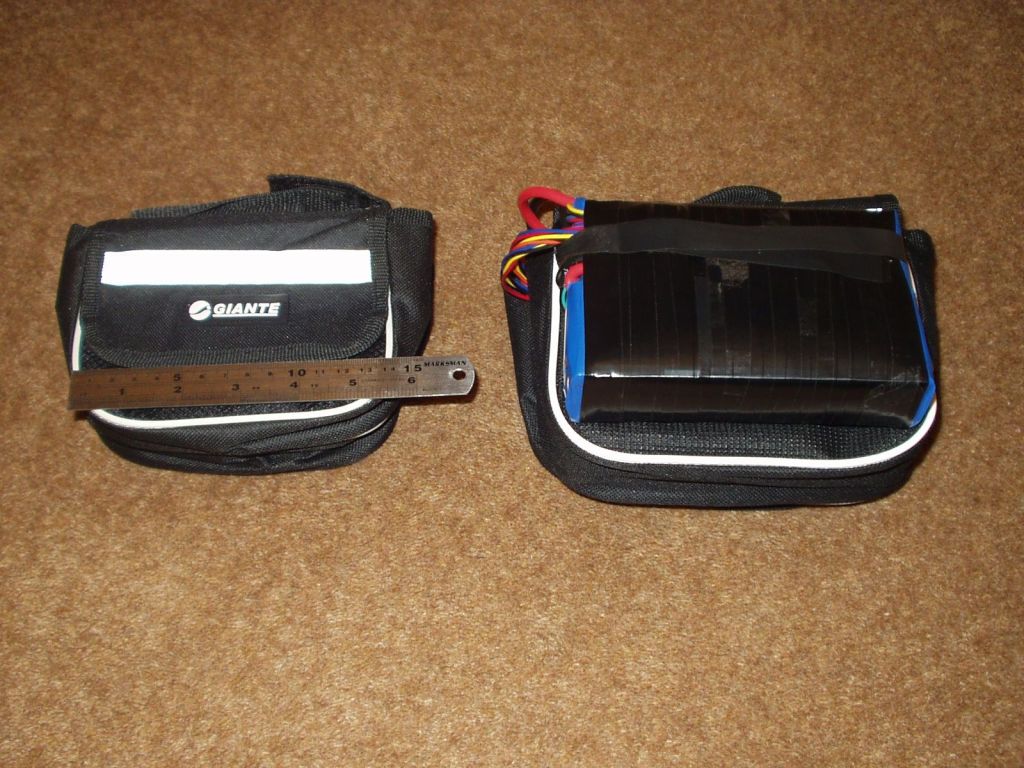
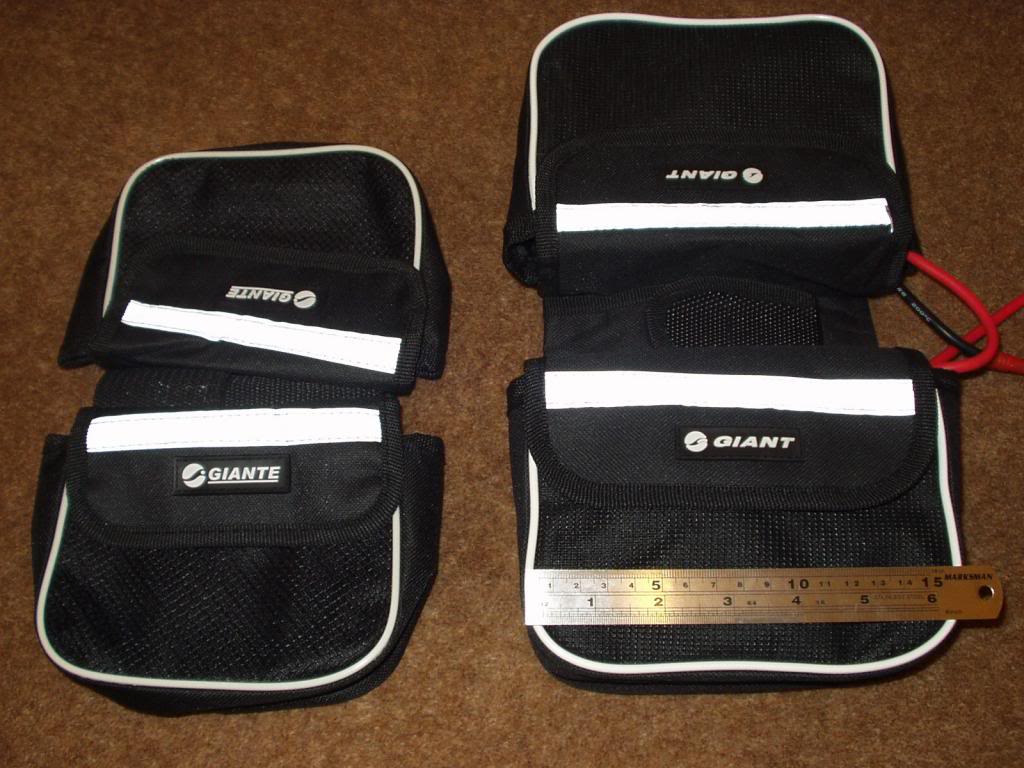
The slightly larger bag on the right made an ideal home for a 51.8V 5Ah pack
(58.8V fully charged) made from 2 x 3s and 2 x 4s Turnigy LiPo soft packs and weighs in at a mere 2.06 kg/4.54 lbs including the same watt meters and battery monitor unit, but this pack is fitted with twin 40 Amp fuses
(wired in parallel) to safely deliver up to 80 amps of continuous current output.

Voltage pros and cons:
A 36V 8Ah battery has more stored energy than a 24V 10Ah, which should provide a greater range if limited to produce the same power output, but it will probably be slightly heavier too.
A 36V pack will give you assistance up to a higher speed than a 24V pack, allowing you to maintain your speed for longer on hills and therefore climb them quicker.
Two identical 24V packs can be connected in parallel to double the range, or connected in series to make a 48V pack if higher speed is required. Although two 36V packs can also be connected in parallel, they cannot however be used in series, as the combined voltage would be far too high for the GM controller.
Alan