Hi David and

to the forum.
It sounds like you might be wanting a geared minimotor
(shown below), rather than a direct drive motor, mainly because the minimotor has an internal freewheel device which completely eliminates any magnetic drag from the motor when it is not being used.
The internal gears greatly increase the torque output from the small motor, which unfortunately gives a lower top speed, but the minimotor has the advantage of being both smaller and lighter than the direct drive motors.
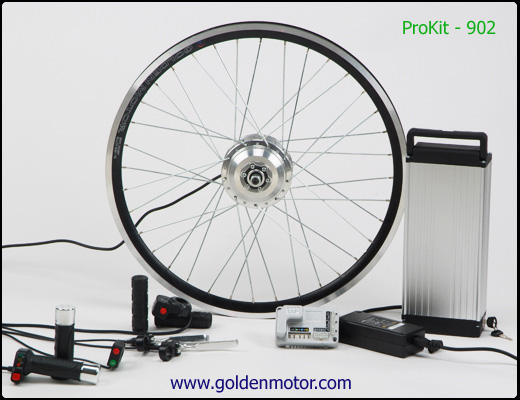
I think the width requirement between the dropouts is ~100mm, but I'm not so sure that carbon forks are going to be suitable for transmitting the axle torque, as the dropouts are not usually designed to withstand any torsional load whatsoever.
I would suggest that you use steel forks to greatly reduce the possibility of dropout failure.

A pre-built wheel would be the simplest option, but if you wanted to build your own, that's entirely up to you.
Perhaps one of the forum members who use a minimotor can provide more information regarding what speed and assistance you are likely to get with different voltages.
This will hopefully have given you something to think about in the meantime.
Alan