As long as your happy this is important.
And yes, ratings are important too.
Here is what I think.
Aussie standards with the 240v mains stuff is better for DC EV's IMO.
Self resetting thermal Breakers use two different expansive spring materials on top of each other formed into a reed and fashioned to be closed contact, when heated one expands more than another creating a bow in the reed and breaks the contact, Click! When it cools the breaker re-contacts.
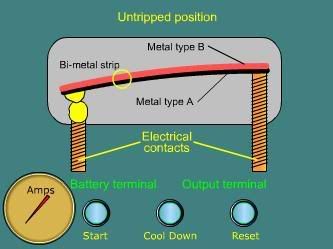
Manual reset method uses electro magnetism "EM" and a piston that breaks the contact when high current is passed through the coil. IMO would work faster than heat. Is this necessary for our needs?

Maybe your temp rated manual reset breaker is based on both types. Without looking right into this I assume this type of breaker is well available.
For a dead short battery protection on a LIPO, I think I would rather the EM type or fast blow fuse, for a wheel lock up, a heat triggered breaker or slow blow fuse would suffice. And the EM type would serve for both short circuit and wheel lock events, as long as it isn't too sensitive and annoying.
I read a "if" breaker has tripped a few times it becomes more unreliable due to the contacts gaining more resistance. To what degree I don't know. But a few resets is better then only one when considering a standard fuse. It may be advisable to replace a breaker if it has tripped a dozen times or so.
The main reason I went to a 50 amp fuse is because I was using a $20 controller when the power supply to that controller was cut REGEN tooK out the fets, otherwise I used no fuse at all.
Over time, nothing electrically we do on our bikes is really continuous, anything before the controller may look smooth but I'm certain caps don't smooth current draw from a battery perfectly, anything after the controller is almost AC, or better labelled as pulsed DC. Even a DC motor straight onto the terminals draws power in pulses, its just PWM can take efficient advantage of a magnetic moments that inductive EM coils like to resonate. Residue magnetism is left over on the low and still active within the coil former. IMO its not just the FET bridge that enjoys the advantages of PWM, more so with motors at low RPM. PWM duty cycle, when short converts to lower voltages in the motor coil as it would with switch mode regulation.
I once had a theory voltage boosting via an inductor to a motor would yield better speed performances, but this was flawed on the grounds that the inductance of the motor and a high originating voltage served the exact same purpose more efficiently based more upon current consumption and torque modelling instead.
I stray off topic a little here.
The linkage between the battery and controller caps is all interesting to me.
My switch for instance is rated at 240v AC, 30 amps continuous and possibly 50 amps peak. My bike is lucky to draw 14 amps most of the time so Id rate my switch at
100v 50v 30 amps.
I was always lead to believe AC transmission was better than DC but, upon reading, DC seems to be better but only on the bases that the DC endpoint is converted by an inverted AC load, DC transmission lines is just a link for the inverters to milk power from. Interestingly this is similar to the supply a controller is given and takes. Advances in EV tech would inevitably take advantage of these inventions if it needs to.
Filtering only seems to take out ripples to supply a device for practical operating specifics. Instead of current ripples between 0 and 30 amps cap filtering transforms ripples that more approximate from 20 amps to 10 amps respective of duty cycle, load and voltages. I'm sure my ball park figure are a bit off the mark, however you already know what I mean.
Unless its a simple battery and constant current load like a heating element; maximum, minimum, averages, time, and frequency works its way into the math when considering current demand.