Although it will work without a contactor, it does not sound like a good solution.
To prevent the main contacts inside the contactors from arcing themselves together you need to use some form of pre-charge system to charge up the capacitors in the controller before the contactor is energised.
You could use a simple momentary push button switch and suitable resistors to pre-charge the controller before manually switching on the contactor. If you have a voltmeter connected between the controller main feed and ground, you would see the voltage rise when the button is pressed until it is near battery voltage and ready for the contactor to then connect without arcing.
I would suggest using a resistance of ~1000 ohms with a 10 Watts power handling capability.
Four of these 1000 ohm 5W resistors:

connected in a series parallel configuration:
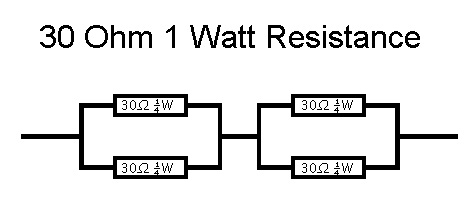
would be equivalent to a single 1000 ohms 20 Watts resistor which would limit the pre-charge current to ~0.1A, so you wouldn't need a heavy duty push button switch.
I am surprised that the 300A fuse has blown, as I would still have expected it to withstand the initial high inrush current surge when the controller is connected to the battery without first being precharged.
But, as the contactors are apparently unable to withstand this high current burst, perhaps it is also too much for the fuse to withstand.
As you cannot easily dismantle the stuck contactors to separate the contacts, you may be able to shock the contacts apart by tapping the flat end of the contactor
(the opposite end to the connectors) against a solid piece of wood.
Hopefully a little tapping
(or heavy duty bangs) will eventually cause the contacts to separate.
Make up a simple circuit with a battery and bulb connected across the two main contacts and keep tapping/banging the contactor until the bulb goes out. If it doesn't work on the flat end, try banging it on the sides instead.
The contactors are currently unusable as they are, so you have nothing to lose by trying to get them working again.
Alan