The GM spokes have an outside diameter of 2.2mm, which is 0.1mm smaller than 13 gauge
(2.3mm diameter) and mine measure 186mm long from the inside of the elbow to the end of the thread.
When spokes break, it is usually because they are inadequately supported around the elbow and are failing due to metal fatigue caused by constant flexing of the spoke's elbow each time the wheel rotates:
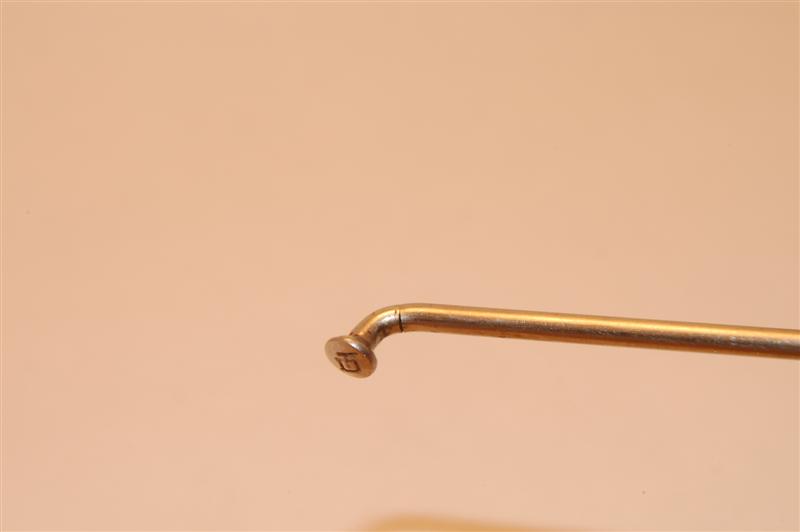
I recommend
Sapim 13/14g Strong Butted Spokes, which are slightly thicker around the elbow to ensure a better fit in the motor flange holes, but are more importantly thinner along the majority of their length, which allows a greater linear stretch under tension:
A common reason for spokes to fail on hub motors isn't because the motor puts extra strain on the spokes, or because the spokes aren't a thick enough gauge, it's because of fatigue failure from spokes that aren't held snug against the flange. If the spoke bend radius is too large or too far from the head, then it can flex up and down at the bend with each wheel rotation, eventually causing it to crack and fail.
This problem has been legendary with overseas built hub motors, and we had some Crystalyte shipments where about half the customers would experience spoke breakage on a recurring basis. Ideally the distance between the head and the bend in your spoke will match the thickness of the hub flange, and you won't have problems. But if not, there are two ways to address the situation. One is to insert a washer under the spoke head. The second way is to lace the wheel in an over/under pattern, such that the spoke tension compresses the bend part of the spoke into the flange.
I have also used spoke washers in the past to ensure that the inner radius of the elbows is held nice and tight against the motor flange:

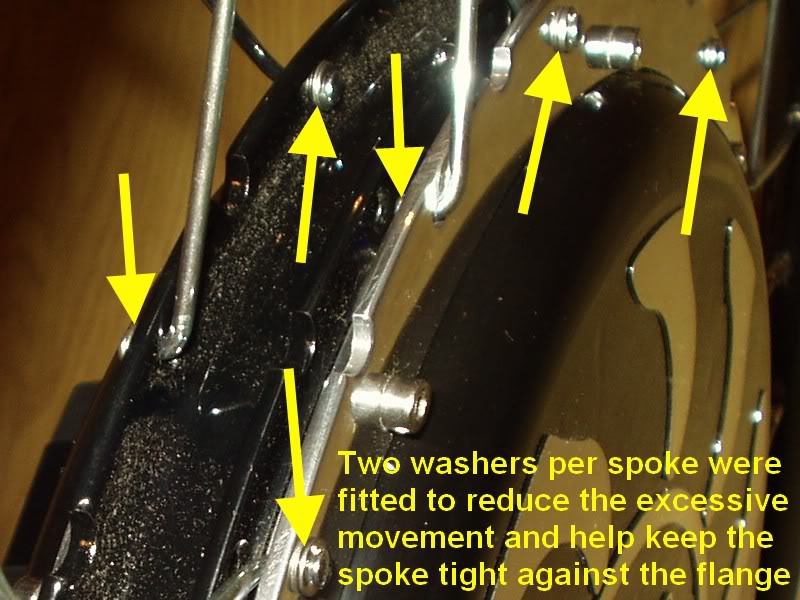
I have been using GM hubmotors
(with their original GM spokes) over the last 9+ years and have not even experienced a single broken spoke during this time. If spokes are properly supported at their elbows, and kept correctly tensioned, they are unlikely to fail.
Alan