Hi Adam and

to the forum.
1. It sounds like the problem is with the electrical contacts inside the contactor not making a good connection when the solenoid plunger is energised. As most contactors are sealed units, it may need to be replaced.
You can try operating it intermittently
(lots of times) to see if the continuous movement will eventually clean the contact surfaces, but if it's caused by plastic debris trapped between the contacts, you may find that it won't make any difference.
2. I suspect the HPM3000B has 8 magnets
(4 pole pairs) the same as the HPM5000B, and your Hall sensor markings would also seem to indicate that there are
4 pole pairs.

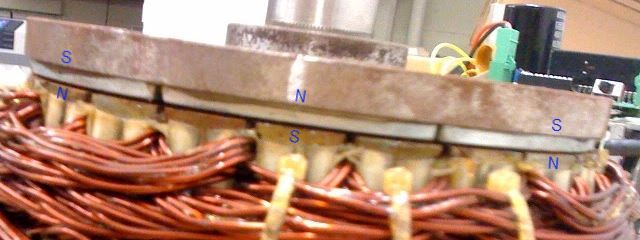
Set the "
Number of pole pairs" parameter to
4 and see if it sorts your problem.
3. Your throttle seems to be working correctly and your throttle parameters seem to be correct for a twist throttle:
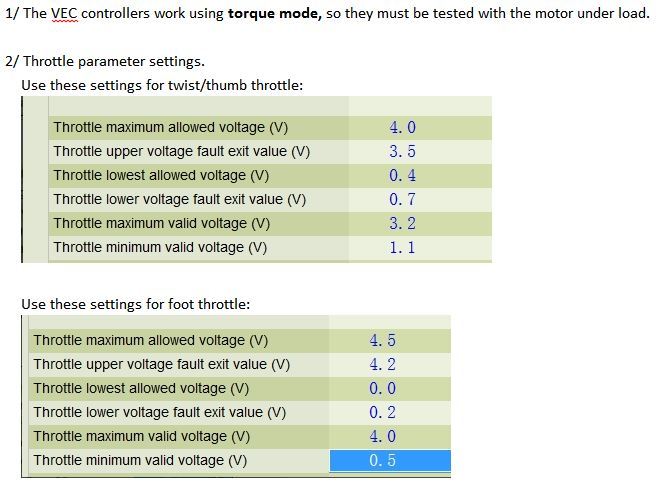
4. From what I can see, the Hall sensors all appear to be working correctly,
but in a slightly difference sequence (G-Y-B) compared to the HPM5000B
(Y-G-B) for clockwise rotation.
Hopefully, entering the correct number of pole pairs will cure the problem.

Please let us know if this works.
Alan