Hi Don,
If you read that post again, you will see that I actually recommended
39.5Nm, or 28.76 foot pounds, so if you are happy to tighten yours to 40ft/lbs it should be plenty tight enough for the standard axle nuts.
As I've previously mentioned, I always tighten the axle nuts by feel, as I can usually "feel" when a nut is approaching its yield point.
I will admit that I probably tighten mine a bit more than they need to be because I have steel frames and I run a modified Pie at up to 50 Amps with no torque arms fitted.
I have previously
measured the torque output of my modified Magic Pie, which worked out to be ~93Nm @ ~66Amps. Therefore a standard Magic Pie will probably produce ~42Nm of torque @ 30Amps.
My modified controller was eventually pushed to it's limit, but before it finally died, it delivered a whopping 97.75 Amps to the motor:
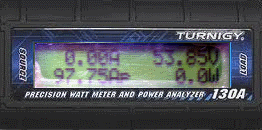
As torque is proportional to the current, this should theoretically have produced almost 138Nm
(101ft/lbs) of torque, which my overtightened axle nuts were able to withstand without allowing the axle to move within the frame dropouts
(and that was also without any torque arms fitted).
The most important thing to consider is that the torque on the axle is not one directional, as each time you engage regen, the torque on the axle is applied in the opposite direction to when the motor is being powered.
Any movement at the axle fixings whatsoever should be avoided at all costs, as it will inevitably result in the loosening of the axle nuts.
I regularly put a spanner on the axle nuts just to check they are still nice and tight and I haven't needed to retighten them yet, so presumably nothing is moving where it shouldn't move.
Alan