So much depends on what you can measure more than what is written on the web site. You could draw wll over 60 amps with this motor.
The motor is 3000 watts, divide this by the voltage 48v = 62.5 amps. You do not need a 500 amps controller for this wheel to run 3kw. 48V @ 500 amps, 48v* 500= 24000KW. So who knows howm much you are drawing from a battery only designed to deliver 1440 watts over 20 hours. I would guess about 90 amps your running. 4800 watts. Too much current for this battery and motor. All motors can draw up to 3 times it watts when starting and there need to be a shunt to stop this inductive inrush. Idealy you need a high performance lithium pack in the capacity range of 60ah+ and modify the controller to limit to 100 amps max. I would recomend a 100ah lithium pack and steer clear of the SLA's. SLA will become a money hole in your pocket and already your not happy with the results.
SLA are not designed to do high loads at 2C-3C they can do it for short bursts but if continuous you will see a large drop on the battery.
You may witness 12v an SLA drop to 10.75v with at 3C in a very short time. SLA are not designed for high current and long duration discharges. .
Besides I would guess you could be pulling nearly 100 amps with that contoller on the motor. I can make an SLA last for 6 mths @ 1C they should last for 3 mths at 2C but most controllers wont let it work for more than a few weeks because the damage you create A 2C makes the SLA perform very bad in only a short time..
You are messing with specialist high powered gear, you need specialist battery..
A good rule of thumb.
Measure your amps when you load the motor, mutiply this by the voltage you witness on the battery at this load, and you have your watts.
mutiply 12.8v by 4 this is 51.2v and see how much the voltage drops on tha battery when you stress the motor running. Say you measured 100A on load, and you see a 5v drop on you pack. Then multply 5v by 100amps that is 500 watts of power down the drain, it is heat inside your batteries, and causes much damage..
Now multply you AH batteries by the nominal voltage 48v.. 48v* 30ah = 1400 watts your battery might give, but this is rated over a 20 discharge rate..
Minus the 500 watts from your 1400 watts and your battery is capable of only 900 watts of power total. This is not really true, it gets even worse, but please read on.
View this image, it does not matter the AH, it matters the C rate.
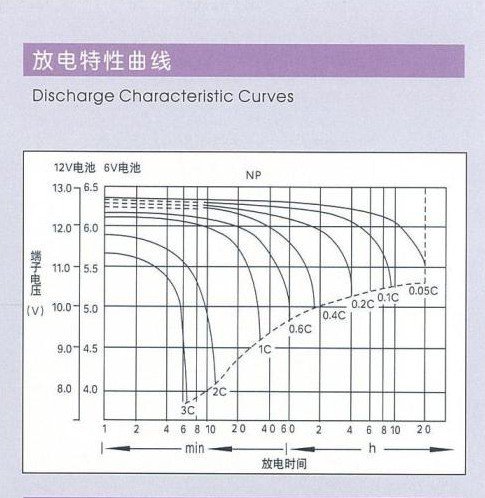
If you take the current you draw and divide by your amp hour you will get your C rate. If you draw 100 amps, you divide this by 30ah and you will have 3.3333C
Now look at this image again. You can see that a lead acid battery will only run for about 4 minutes to 10.75v at 3C and this gets worse at 4C As you can see how much less time it takes to discharge, the more C you are taking from your pack. Sure there is plenty power left, but all the controller sees is the voltage, when it slumps bad. the controller will Low voltage cut (LVC) at 47v if it is designed for Lithium and it will cut at 43v if designed for SLA.
Most controllers are now designed for Lithium batteries.
most 30ah batteries is rated to a 20 hour discharge or they are much heavier for such heavy tasks 30ah @ 20hr discharge = 1.5 amps. 1.5A/30ah=.05C
30ah @ 3c = 90 amps * 48v = 4320 watts/ 60mins * 4 mins= 288watts your SLA can deliver before it hits LVC. You will only be able to get 20% of the packs rated output if you draw 100 amps and 288watts would barely get this 3KW motor going.
My 48v 15ah Lithium pack is rated at 1C, it is capable of delivering 720 at 15 amps. Many use it to 2C. This is 30 amps. And my light bike only draws 2C for a very short time. I think I couldget closer to 90% of my rated capacity.
Very expensive Lithium cells can do up to 10C, 30C max. Even a 10ah A123 specialist EV pack weighing under 8kgs might do better watts than a SLA 30ah pack that weighs 35kg with high powered motors..