One of my HBS36v GM motor has done me some hard work and after some encouragement to load the ebike to its max, one night the wife brought back one very hot smelling motor.
I hosed The HBS36 down to cool it.
After a week the hall sensor that was replace failed and I had to put the bike into the dry dock for some work
I found the windings were very dark and the stator had melted plastic insulator melted from the teeth.
Before and after shots.
This motor was pushed time and time again way past its intentional designed limits so in essence ive been very happy with it performance. It was still functional before I undressed her but as you can see it was on its way to the grave.
HBS WYE Star configuration.After some good advice from Rolf here as to the winding order, observing the motor and surfing google I came up with this winding pattern. It is the same as Rolf suggested but drawn out as it is configured in the HSB GM motor.
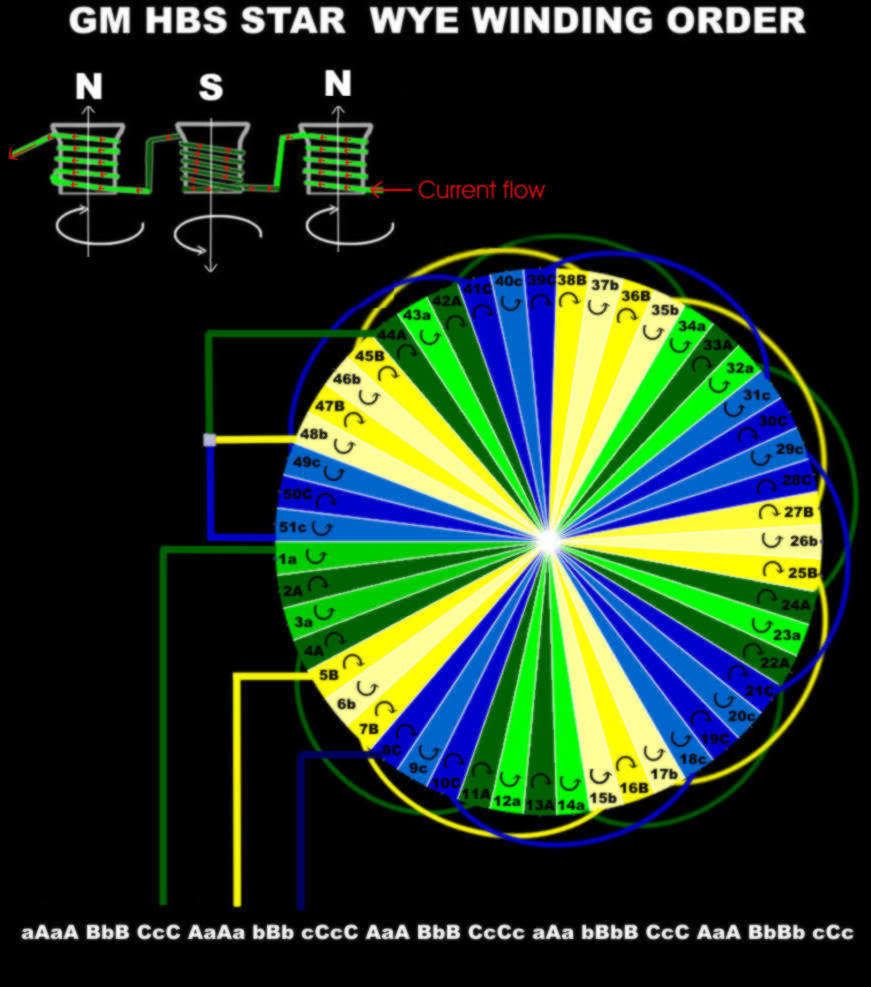
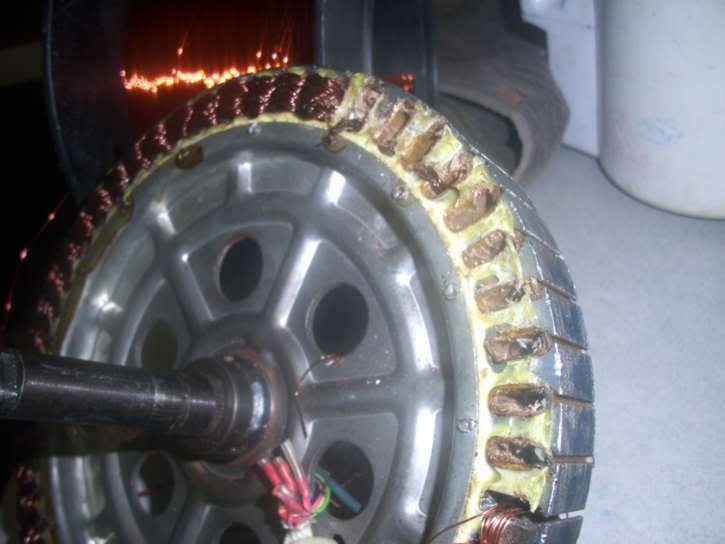
I gots my high grade enamel copper and some off cut winding paper. $33 dollars so far. The guys at HQ industrial windings have offered to dip this for $10 when I've finished
It was very hard to get these windings off. I used a small flat head screw driver to part the winding down centre of the slots and drilled a hole in between them with plenty of copper between each slot and the drill bit as to make sure I didnt flare the slot layers apart. Then used pliars to pull out the windings.
Once I broke the first winding I knew then there was no turning back.
As you can see the plastic core insulator around the outside of the slots is melted from overheating. I will remove this and replace it with the paper I got from HQ.
The grade of copper I got is rated above 180~200 deg C (in background) and it has a nice redish tone to it.. The copper on this hub is about 5 shades darker than it was when the hub was new due to the excess heat from overloading the hub.
I haven’t got a good count of the turns yet but last count was 7t6p on the HBS36. I think 42 strands surround each tooth. I will get a certain on this before I finish.
The paper in between the coils and stator was still in good shape and in good faith GM should observe this for future builds as indeed the paper out performs the plastic by a good margin.
IMO paper in place of the plastic mouldings would still be an improvement on the already hardy design. I really wouldn’t say what happened was due to a flaw in the design, not at all, I just I see room for better design.
GM should look at the data coming out of this work very closely because they will not find many GM motors that has been pushed so hard in such a way.
This damage has not been done by a 86v over volt this has been done by sheer loading of weight by means of a trailer carrying lots of shopping.
This is how I plan to tackle my problem.I’ve done a bit of restoration and removed the melted plastic stuff.
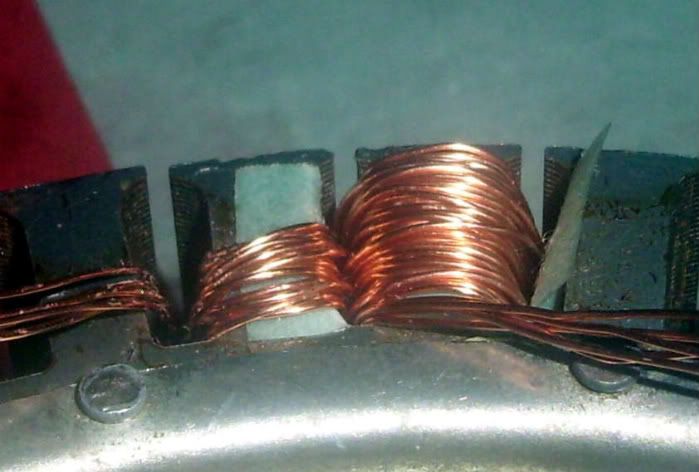
Another test wind with some lower temp WW4016 enamel magnet wire "I have to experiment with". This is a 7p 8 turn wind with flat layered incrementing winding style from top to bottom on the first coil. I am contemplating doing a 8p 7t.
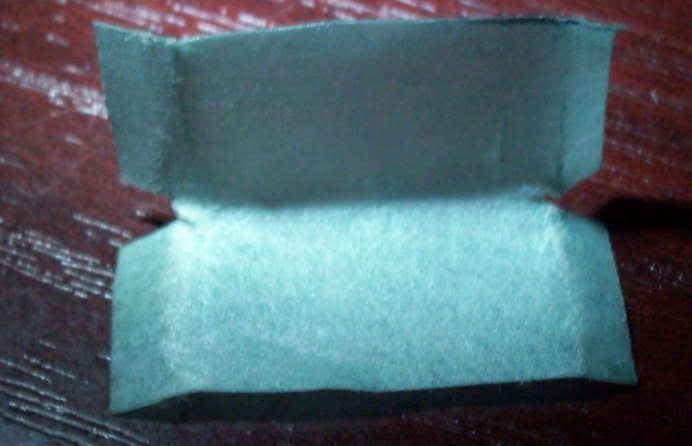
High temp winding paper cut into rectangles folded into V's with a 5mm nick in the middle to allow half flaps to overlap each other in the centre of each tooth.
I have a 1kg of that higher grade enamel wire for the real job.
I want some feedback from a few members here before I do anything.
I shall succeed.